Navigating Semiconductor Encoders: A Guide to Selecting the Right Solution
Having access to abundant bandwidth, AI, and advanced optics is undoubtedly advantageous. However, in the realm of semiconductor machinery, the ability to achieve nanometer-level precision without compromising throughput is of utmost significance. Even with a motion system boasting maximum speed, it becomes inconsequential if it cannot swiftly and accurately measure points on a wafer due to extended settling times.
In the high-throughput environment of semiconductors, various trade-offs come into play. While drive systems and structural integrity are important, the encoder holds a crucial role in attaining the necessary amalgamation of speed, accuracy, and stability required for sophisticated processes.
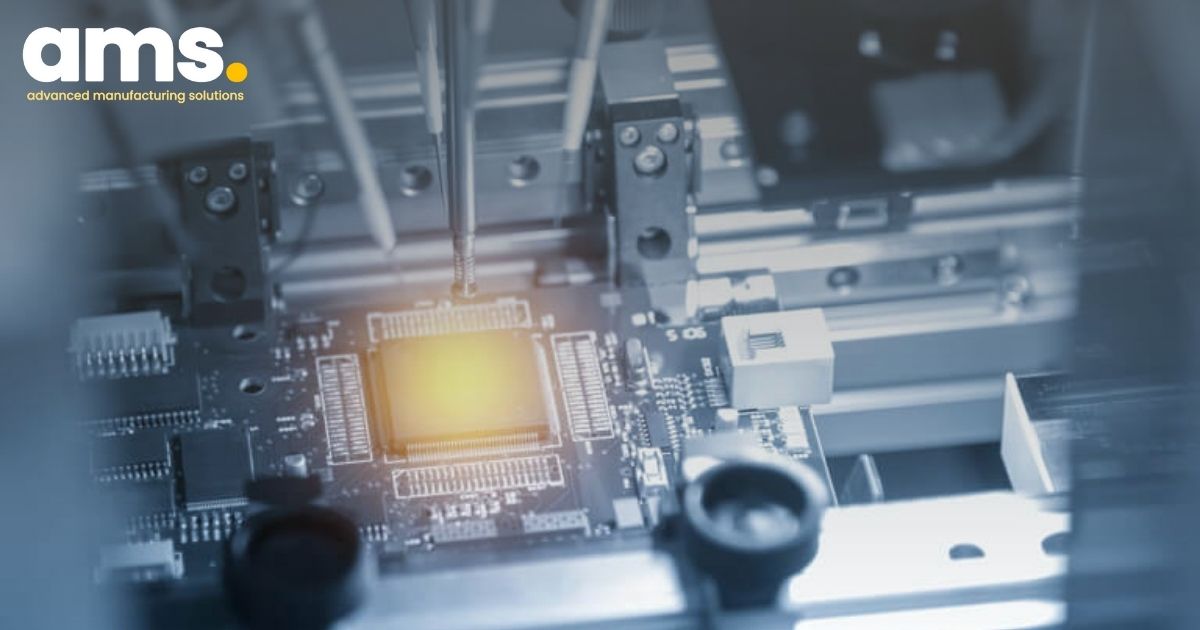
1. Selecting the ideal motion feedback solution for your needs
In order to fulfill the operational needs of machinery, engineers presently have a diverse range of motion feedback solutions at their disposal, catering to both linear and rotary movements. Despite the continuous advancement of new technologies, the factors to be considered are largely consistent across various types of encoders. In the process of selecting the most suitable product, it is crucial to deliberate on the following key aspects:
-
What are the environmental conditions that the encoder must withstand, encompassing factors like vibration, vacuum, and temperature variations?
-
Are there any mechanical constraints that could impact the available space or the method of encoder mounting?
-
What level of precision is necessitated for the specific application?
-
At what speed is this requisite level of precision expected to be attained?
-
How much margin for interpolation error can be accommodated within the operational parameters?
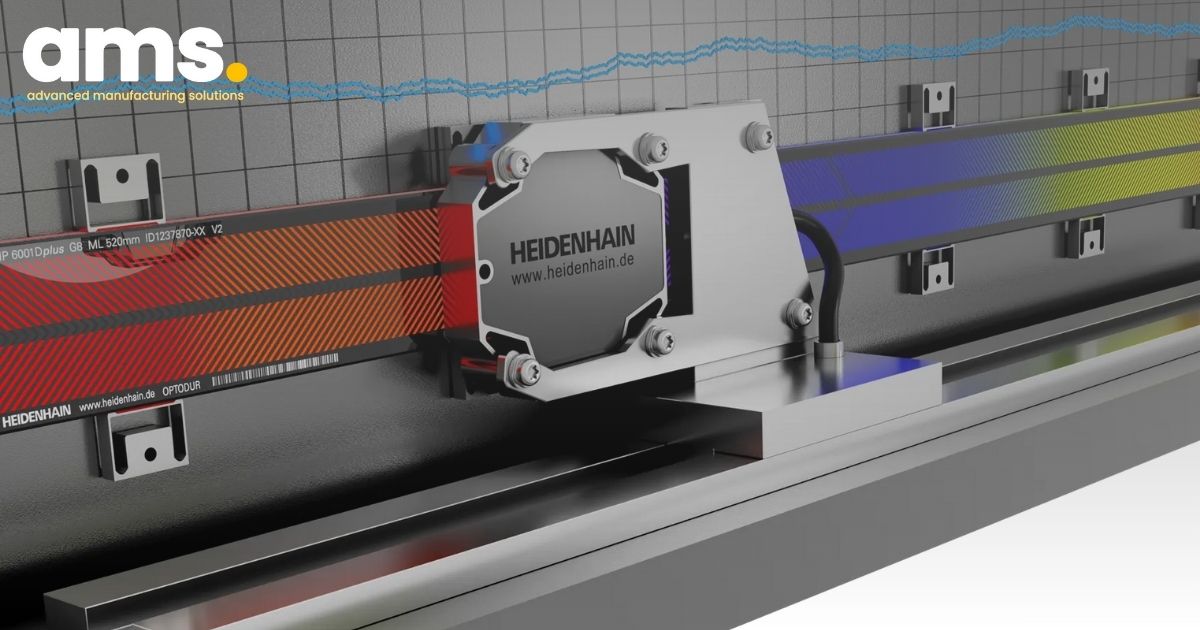
2. Reviewing the specifications: a crucial step
Once these factors have been established, the available options can be effectively narrowed down. One of the initial considerations involves selecting the type of encoder, which may include mechanical, optical, magnetic, or induction variants. For instance, in scenarios where an operation occurs within a vacuum and space is a limiting factor, the viable options may be constrained to products like the Numerik Jena LIK 41 or KIT L Series. In the specific case of a vacuum application demanding high precision, such as in photomask fabrication, the suitability of products like the LIF 471V or 481V would need to be assessed, taking into account the interface requirements. Furthermore, if extreme accuracy is paramount, the LIP 481V might be the more suitable choice. Subsequently, a thorough evaluation of additional specifications presented in the catalogue becomes imperative in order to make a well-informed final decision.
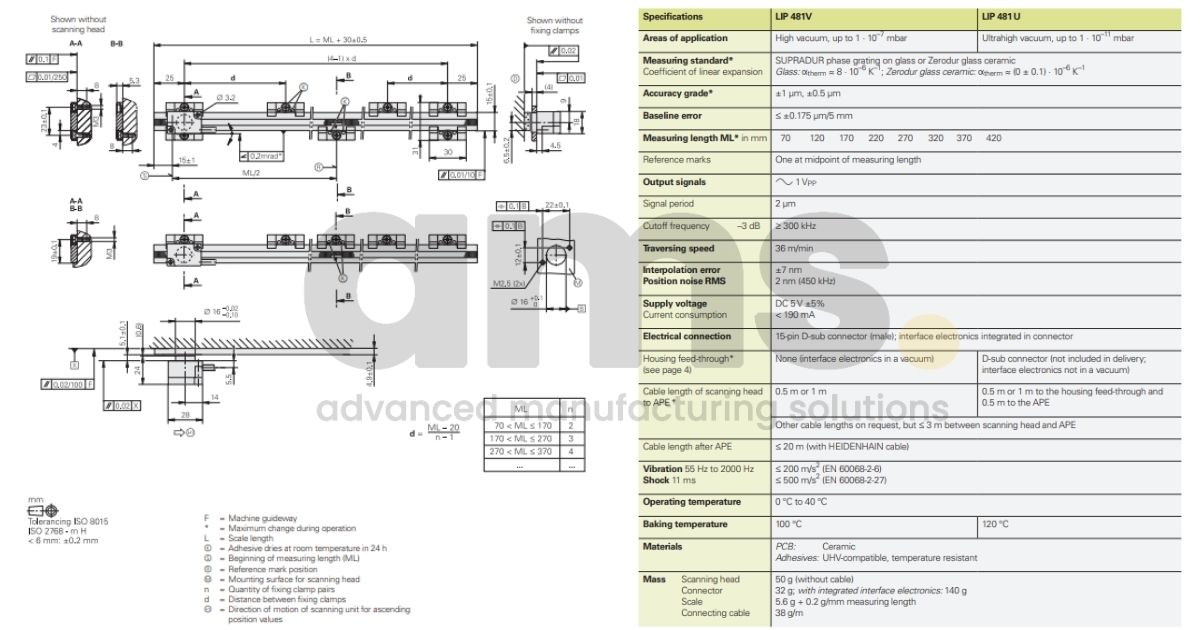
3. The importance of the measuring standard
Whether it pertains to linear or angular motion, another critical aspect of an encoder's functionality lies in its measuring standard, specifically the graduation on a scale tape. While the line count of a scale garners significant attention, the manner in which these lines are generated and applied to the scale at precise intervals also holds great significance. This aspect is so pivotal that specific proprietary processes have been developed to address it. The OPTODUR, SUPERADUR, and METALLUR designs are engineered to create 3D structures with exceptionally high edge definition and an inherent resistance to contamination, which could otherwise disrupt semiconductor processes in both the front- and back-end stages. Furthermore, these structures exhibit very low height, thus minimizing the surface area available for the accumulation of dust, dirt, or liquid. The graduation of the encoder plays a substantial role not only in immediate performance but also in ensuring sustained and consistent quality over time.
4. Trust and verify: ensuring the right motion feedback solution
Within the realm of semiconductor machinery, every single component is subjected to exceptionally stringent standards, and engineers prioritize parts that inspire confidence in their ability to fulfill the task at hand. When an encoder is chosen, there is an implicit expectation that the product has undergone comprehensive testing and validation to adhere to highly specific standards. Our catalogues contain an extensive array of test results and verified specifications, enabling users to trust in the performance of each component.
For instance, our dedication to rigorous testing is exemplified by our assessment of intervals within an encoder scale, which empowers users to make more accurate performance predictions. This process involves initially defining the interval width for which the accuracy will be stated. Subsequently, the scale is meticulously measured across its entire measuring length in precise, minute steps with the designated interval width. Finally, the uncompensated baseline errors over each interval width are thoroughly evaluated, with the maximum value of baseline error over all measured intervals being specified as the worst value on that encoder.
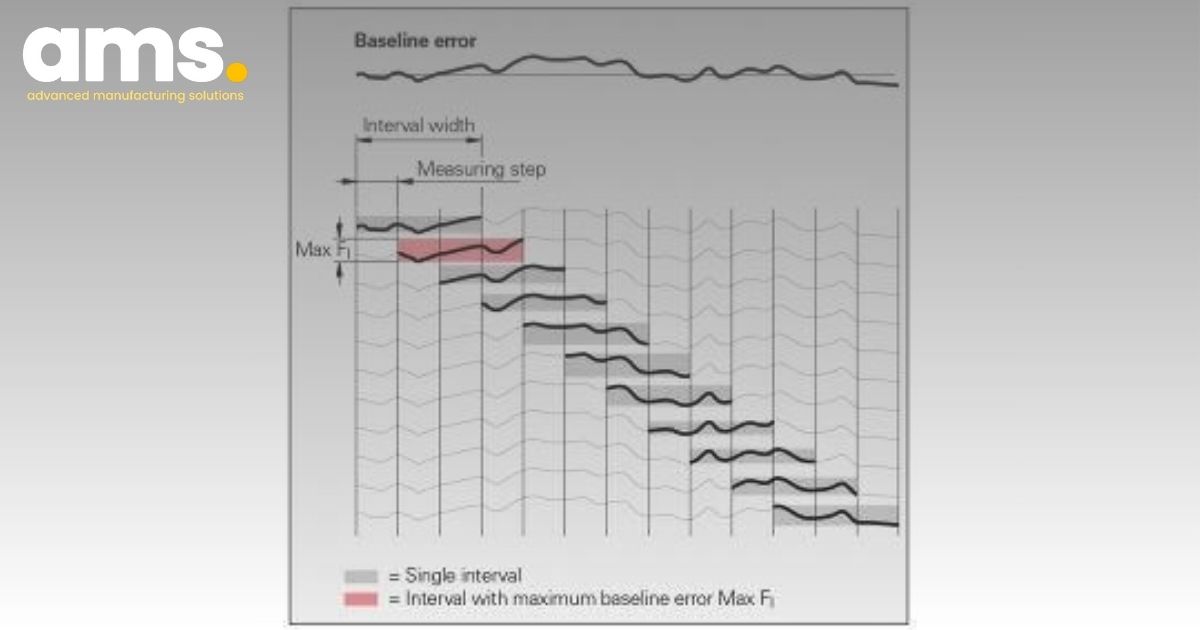
With such comprehensive testing methodologies at our disposal, combined with our unwavering focus on research and development and our proprietary measuring standard, we are able to ascertain and deliver some of the most remarkable motion control performance metrics globally – precisely what the semiconductor industry necessitates. The following are just a few examples of the intricate feedback capabilities available:
5. Exposed linear encoders
HEIDENHAIN exposed linear encoders operate with no mechanical contact between the scanning head and the scale or scale tape.
-
Accuracy grades down to ±0.5 µm
-
Measuring steps of down to 0.001 µm (1 nm)
-
Interpolation error: ±0.01 nm
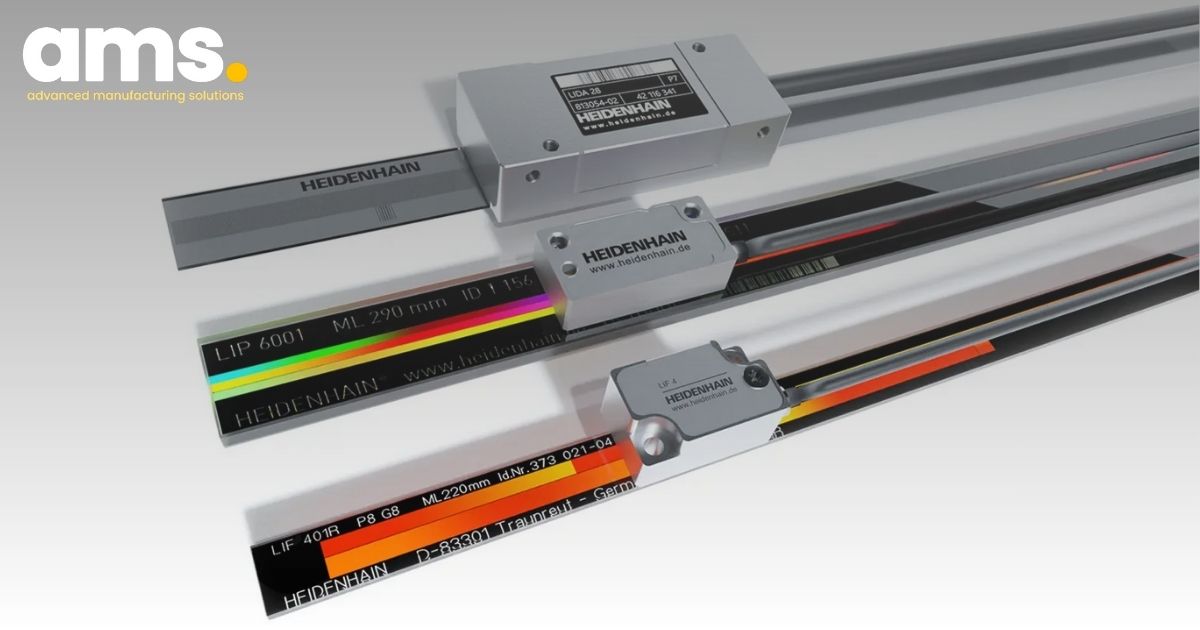
6. Angle encoders
An encoder is classified as an angular encoder when the accuracy is better than ±5″ and has a line count above 10,000.
-
Signal periods up to 360,000
-
Accuracy down to ±0.4″
-
Measuring steps: as fine as 0.00001° or 0.036″ (incremental) or 29 bits, i.e. approx. 536 million positions per revolution (absolute)
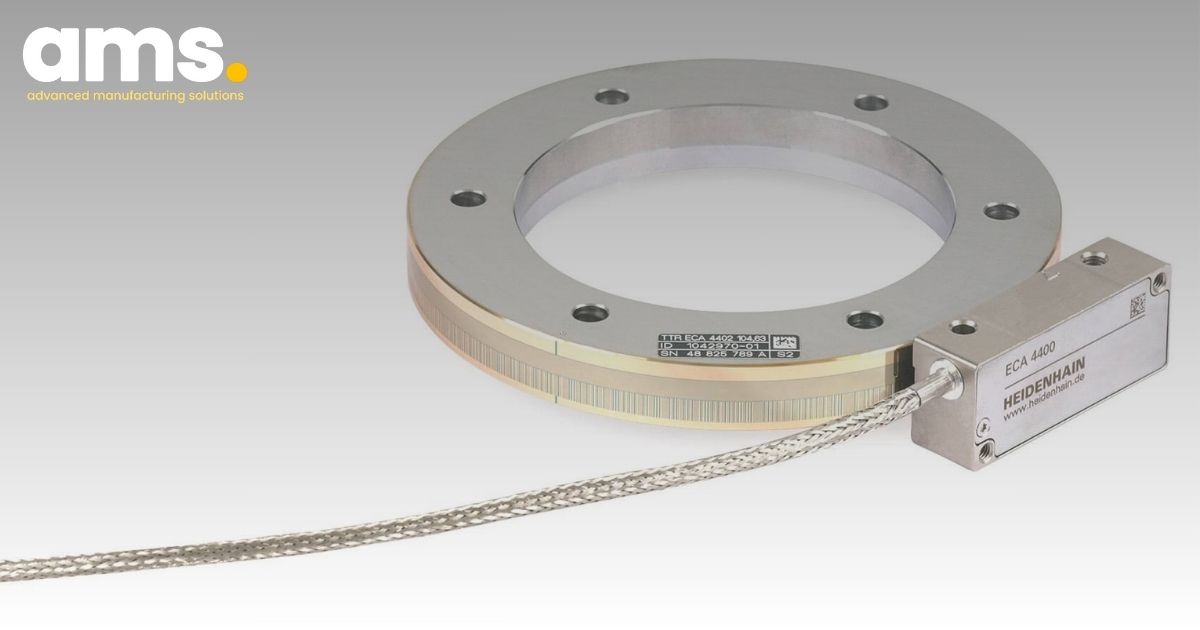
7. Discovering the Advantages of HEIDENHAIN Encoders: Choose AMS Company Limited
When it comes to sourcing high-quality motion control and precision measurement components, one cannot overlook the significance of reputable partners in delivering exceptional products. As we delve into the realm of encoders and semiconductor machinery, HEIDENHAIN stands out as a global leader in providing top-tier solutions that meet the exacting demands of the industry.
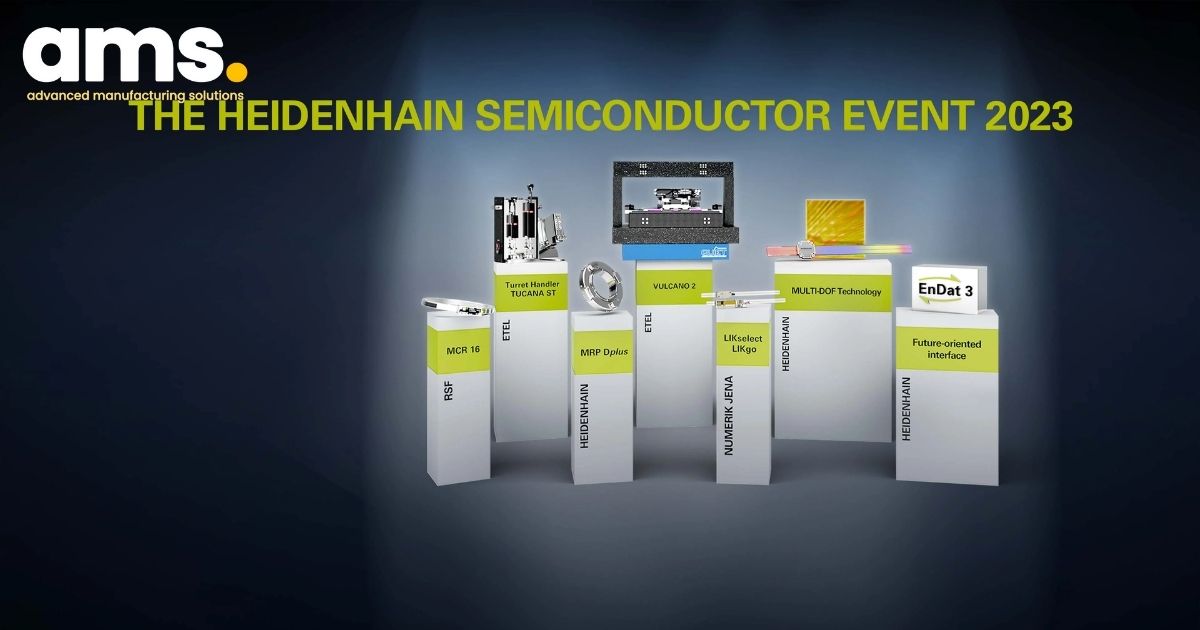
In Vietnam, AMS Company Limited holds the distinction of being the exclusive distributor of HEIDENHAIN products. With a commitment to uncompromising quality, AMS ensures that customers have access to genuine HEIDENHAIN products, which are not only backed by the renowned HEIDENHAIN warranty but also adhere to their comprehensive maintenance policy.
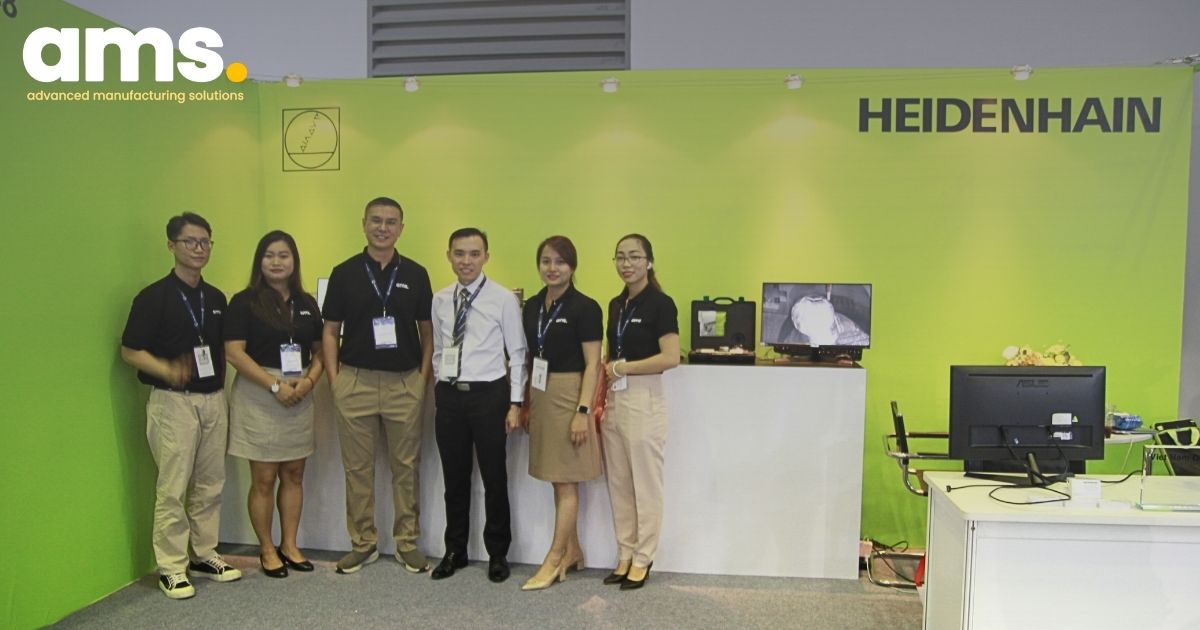
It's important for customers to recognize that when they acquire HEIDENHAIN products from sources other than AMS, they may not be eligible for the full benefits of HEIDENHAIN's warranty and maintenance policy. This means that in the event of any issues with the product, HEIDENHAIN may not be able to provide the necessary assistance, potentially leading to disruptions and additional costs.
To safeguard your investment and ensure that you receive the full spectrum of benefits associated with genuine HEIDENHAIN products, we encourage readers and customers to reach out to AMS for their motion control and precision measurement needs. By choosing AMS as your trusted supplier of HEIDENHAIN products, you can rest assured that you are receiving authentic components and comprehensive support, maximizing the value and performance of your semiconductor machinery.
AMS Company, Ltd.243/9/10D To Hien Thanh, Ward 13, District 10
Hot line: 028.3868 3738/3903 - Fax: 028.3868 3797
Read more articles
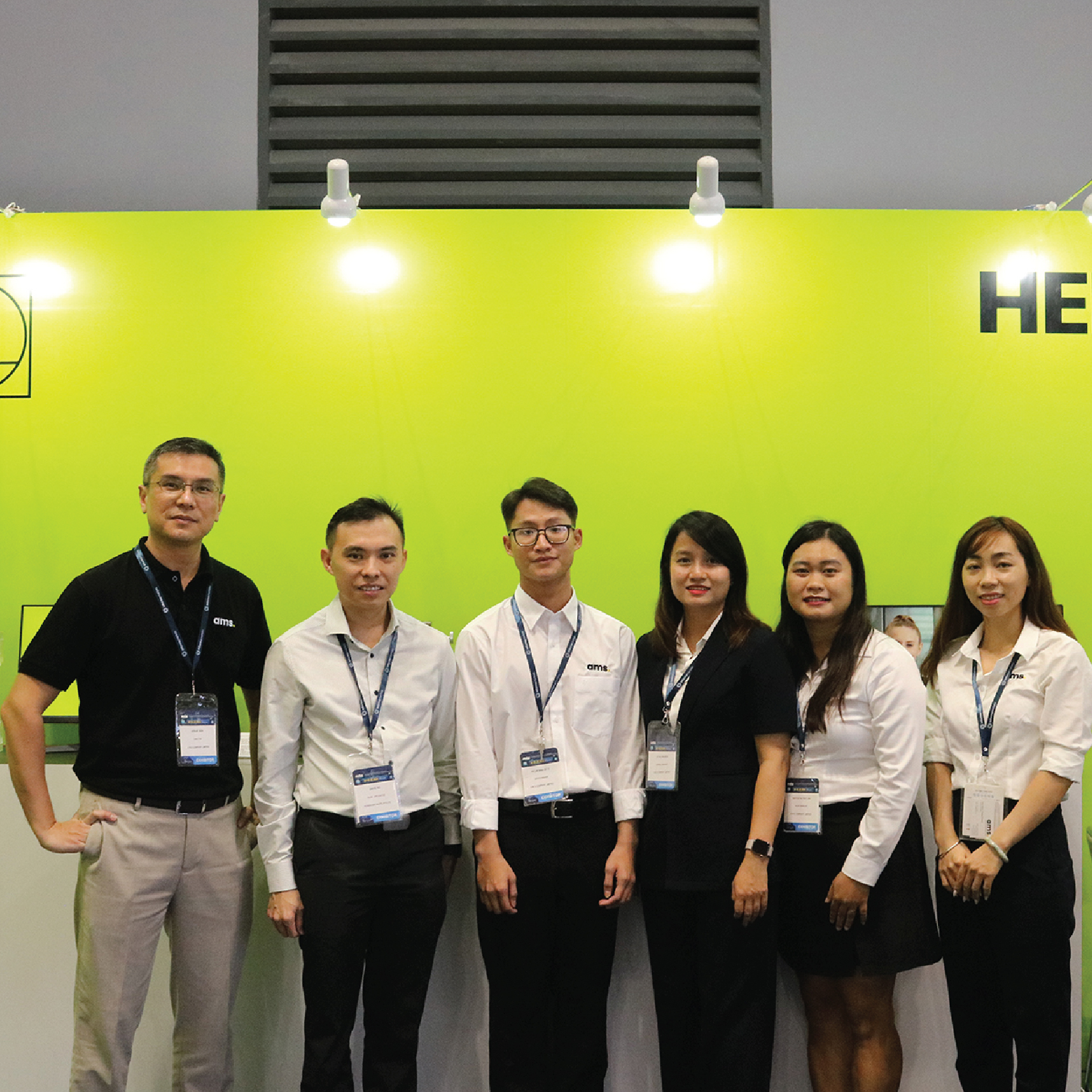
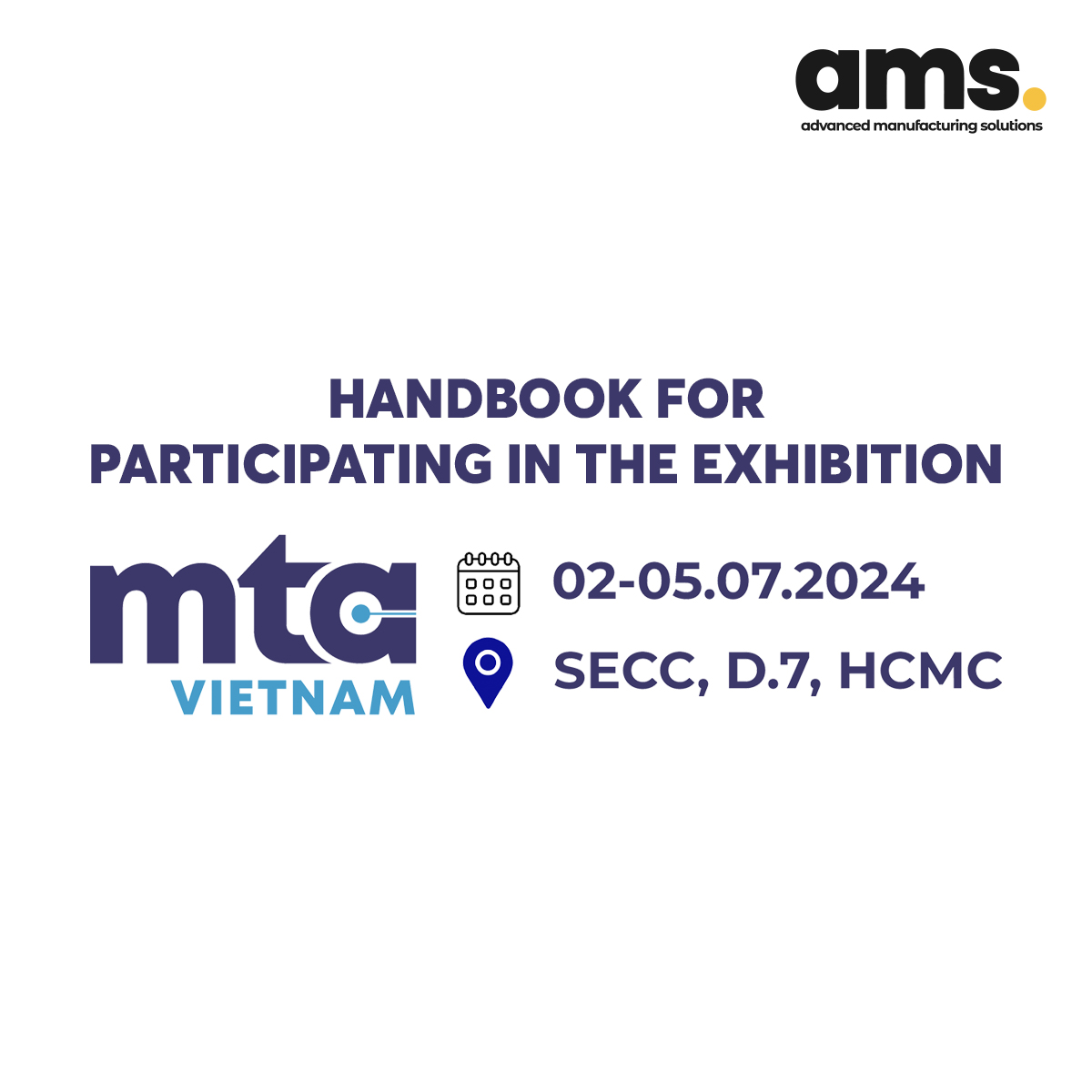
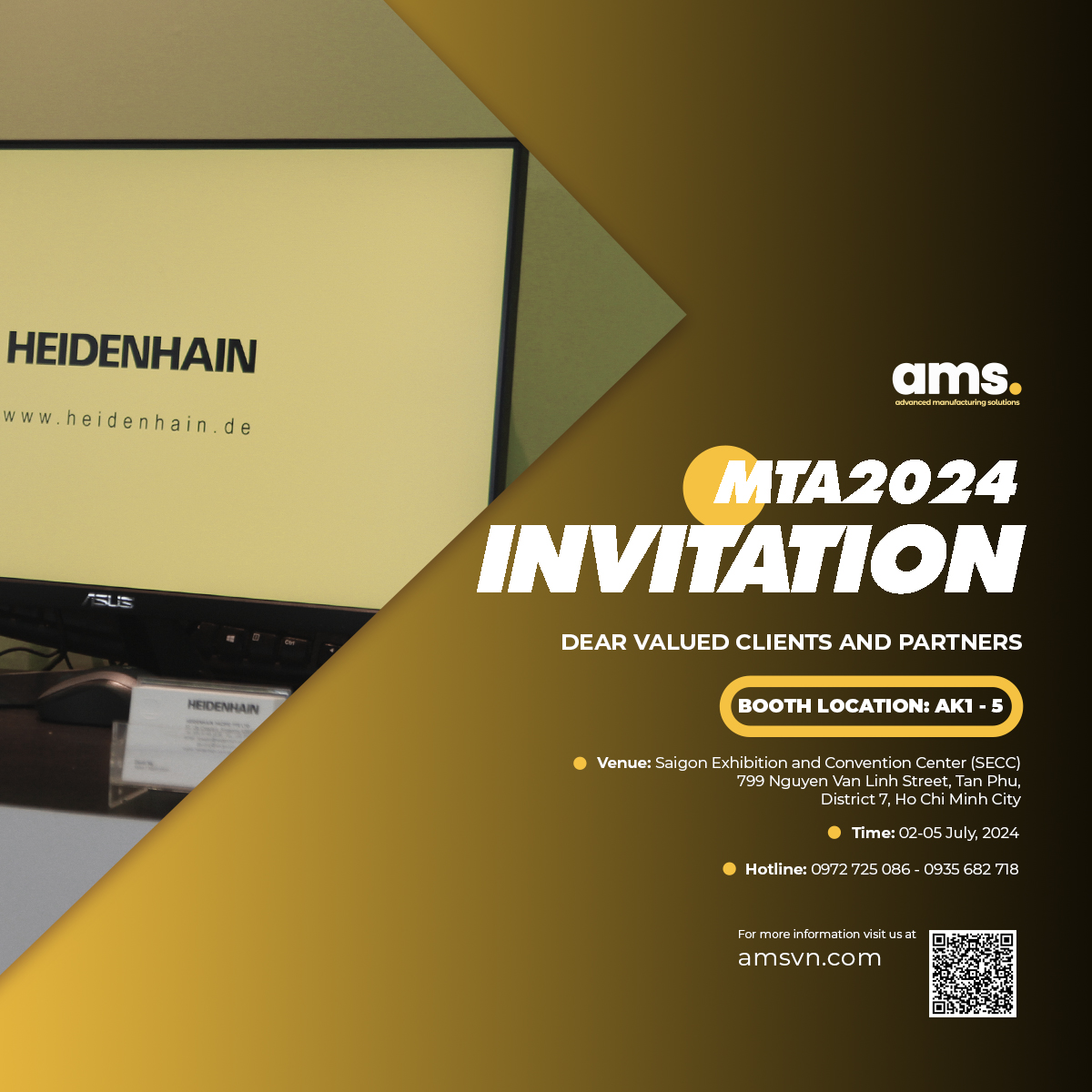