The Essential Role of HEIDENHAIN Encoders in Optimizing CNC Machining Processes
Encoders play a crucial role in machine tools, delivering vital positional feedback to the control system and influencing the speed, precision, and consistency of operations. Linear, rotary, and angle encoders fulfill distinct requirements, such as directional diversity and precision specifications. Encoders can be categorized based on how they interact with light or variations in resistance.
For complex 6-axis machining, secondary encoders are utilized, while grid encoders are employed for high-precision part calibration. In today's world of multi-axis, CNC machinery and small-production runs, the modern machine tool heavily relies on a harmonious blend of speed, accuracy, and repeatability. The efficacy of a metalworking operation hinges on these factors, as a single defective part not only leads to increased material expenses but also disrupts downstream processes, impacting productivity and schedules.
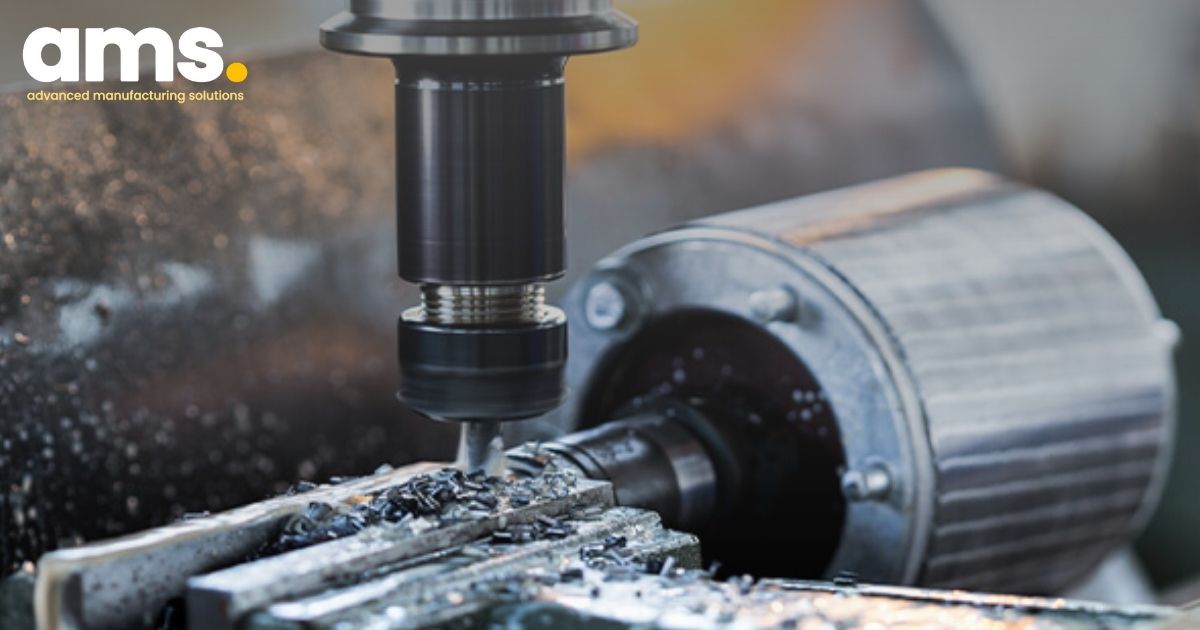
Encoders are instrumental in ensuring the ideal combination of speed, accuracy, and repeatability by providing positional feedback to the control, essentially encoding the position or movement for comprehensible interpretation by CNC controls and operators.
With a rich history of leadership and innovation in motion control systems and CNC controls, HEIDENHAIN stands out as a premier provider of solutions for machine builders and offers upgrade and retrofit options that enhance metalworking performance.
1. Commonly used HEIDENHAIN encoders for CNC machine control
1.1. HEIDENHAIN angle encoders
Linear, rotary, and angle encoders play a pivotal role in providing feedback within CNC machine systems, facilitating communication between the control system and the corresponding motor. Each type of encoder fulfills the crucial task of monitoring specific motion aspects of a machine, considering factors such as required accuracy and directional versatility. The performance of a machine tool is greatly reliant on these diverse encoder mechanisms, delivering precise and synchronized feedback readings.
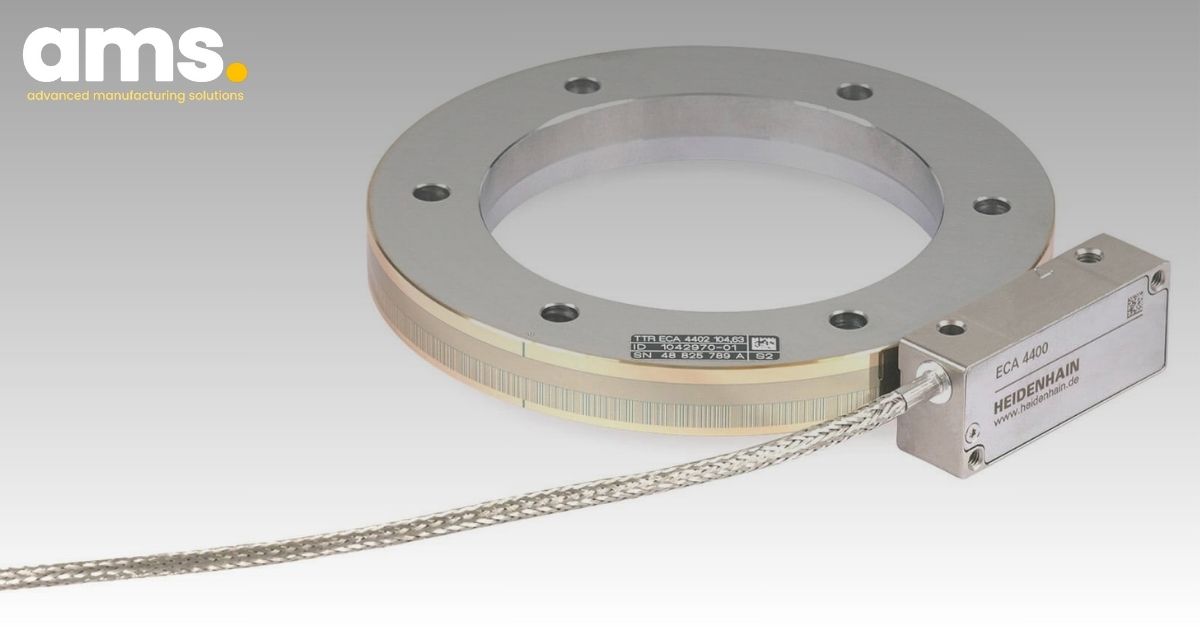
Angle encoders are utilized to meticulously measure the rotational relationship between two components, typically boasting an accuracy better than ±10″ (arcseconds). HEIDENHAIN offers angle encoders that can achieve remarkable precision levels of ± .04″ (arcseconds). This extraordinary precision renders angle encoders indispensable in the advancement of multi-axis centers. Whether these components move simultaneously or independently, rotary table and swivel head designs frequently integrate this type of encoder.
1.2. HEIDENHAIN rotary encoders
Similar to angle encoders, rotary encoders are designed to measure rotation, albeit with a relatively lower precision, usually providing accuracy above ±10″ (arcseconds). While angle encoders specialize in precise positioning, rotary encoders are frequently preferred for speed control applications. Within the machine tool industry, they are particularly valuable for monitoring spindle rotation per minute (RPM), a crucial metric for comprehending and enhancing cost-critical factors such as speed/feed, tool wear, and energy consumption.
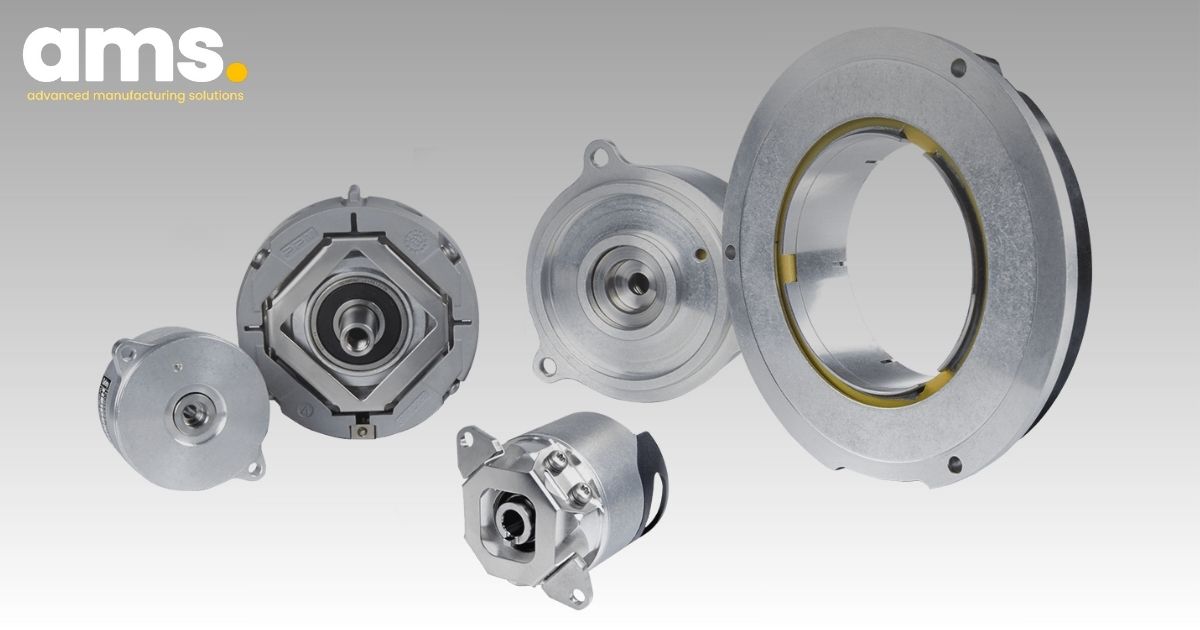
1.3. How HEIDENHAIN rotary and angle encoders work with servo motors
Traditional 3-axis machine centers and lathes, widely used in manufacturing, utilize servo motors to drive tables (typically holding the workpiece) and spindles along their linear X, Y, and Z axes. The motor facilitates movement by rotating a screw-shaped rotor shaft, with the encoder conveying crucial information regarding the speed and distance of the movement.
In the course of extended production runs or abrupt transitions between roughing and finishing operations, issues like reversal errors or axial drift stemming from thermal expansion may arise. As rotary and angle encoders are unable to accommodate axial deformation, which could lead to the production of out-of-spec parts, linear encoders prove to be particularly effective in addressing these scenarios.
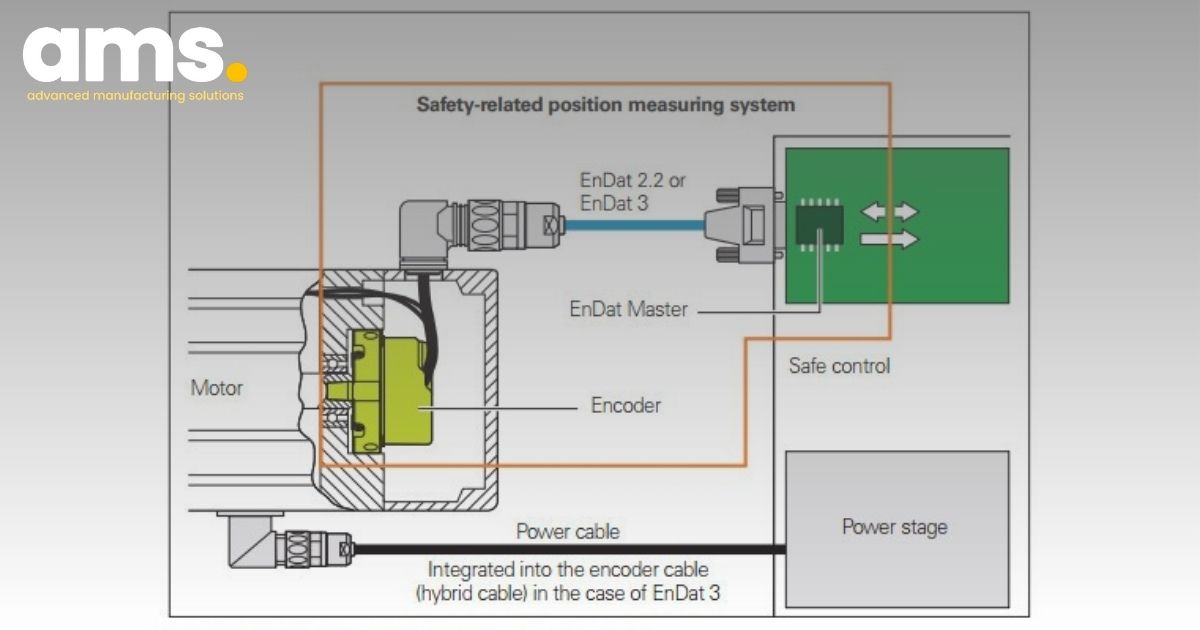
1.4. HEIDENHAIN linear encoder
Naturally, this kind of encoder measures straight-line distance. In machine tool applications, positioning is a much more important consideration than speed, since loads are typically being moved such short distances. Another distinction is between exposed and enclosed encoders. But the enclosed option is the only choice for the extreme conditions in a machining center’s work area. Its sealed unit is mounted on a small carriage that’s connected directly to the machine slide, moving with the table, protecting its sensitive scales and scanning instruments from chips and coolant and feeding precise location to the control.
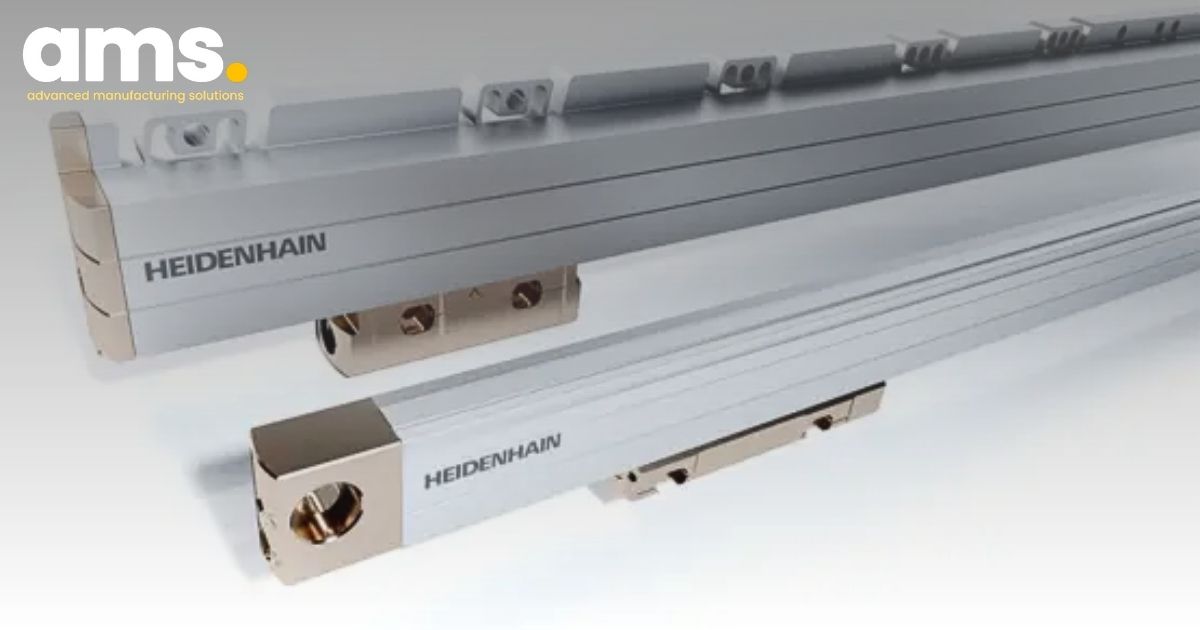
2. How HEIDENHAIN encoders measure accuracy in machine tools
Encoders functionally discern and convey positioning and speed through two key approaches, primarily relying on the interplay between a stationary disc or scale and one that moves with the load. Two primary marking patterns, categorized as incremental or absolute, play a vital role in this recognition process.
The recognition of these markings occurs through a mechanism of light interaction in the case of optical encoders, while magnetic encoders utilize magnetized patterns, where variations in resistance are signaled to the control. Optical encoders commonly employ glass scales, contrasting with the steel application in magnetic encoders. These distinctions are essential in comprehending the modes through which HEIDENHAIN encoders delineate and communicate positioning and speed within machine tool operations.
2.1. HEIDENHAIN absolute encoder
Absolute encoders feature scales or wheels with intricate markings or variations intended for the scanning mechanism to interpret. Notably, absolute encoders eliminate the need for a primary reference point, enabling the immediate acquisition and recognition of specific positioning by the control upon machine startup. This distinct attribute of HEIDENHAIN encoders negates the necessity to zero out a spindle head or work table prior to commencing work, streamlining the operational workflow.
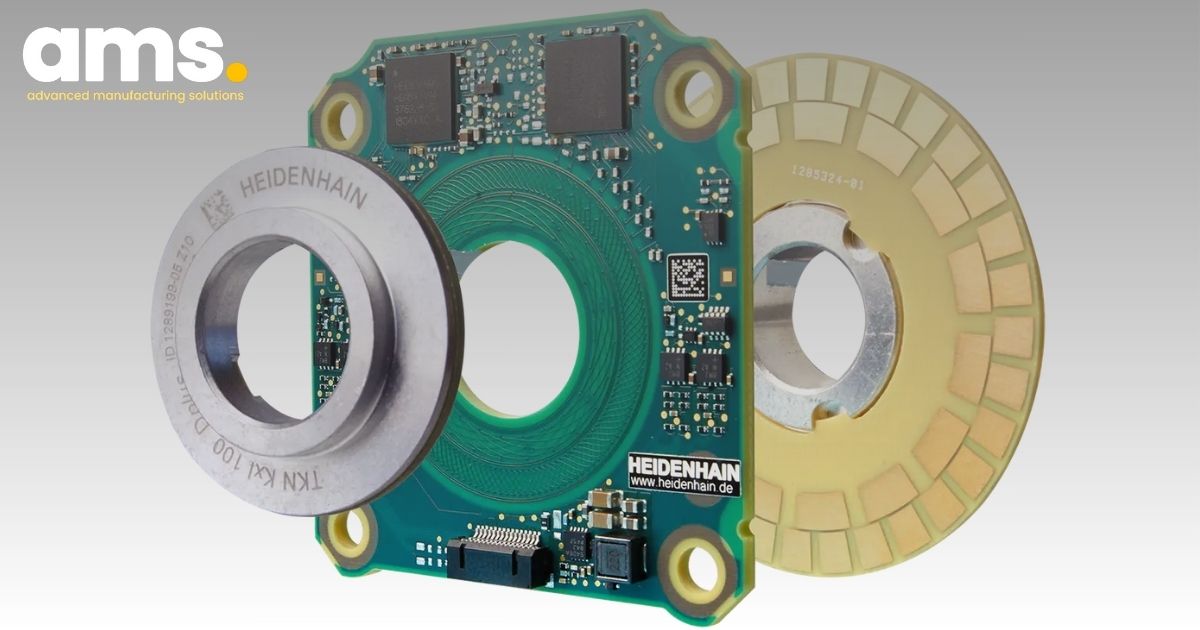
2.2. HEIDENHAIN incremental encoder
Incremental encoders operate on the same fundamental principle as absolute encoders, with the distinction being that instead of distinct markings conveying exact positioning, they employ more uniform gratings to relay relative position. Absolute position is established by reference marks dispersed throughout the pattern. Consequently, machine components employing this type of encoder necessitate the establishment of zero points before commencing work.
Numerous HEIDENHAIN encoders incorporate distance-coded reference marks individually spaced according to a mathematical algorithm. By traversing two successive reference marks, the electronics identify the absolute reference marks, aligning with the operational capabilities of HEIDENHAIN encoders.
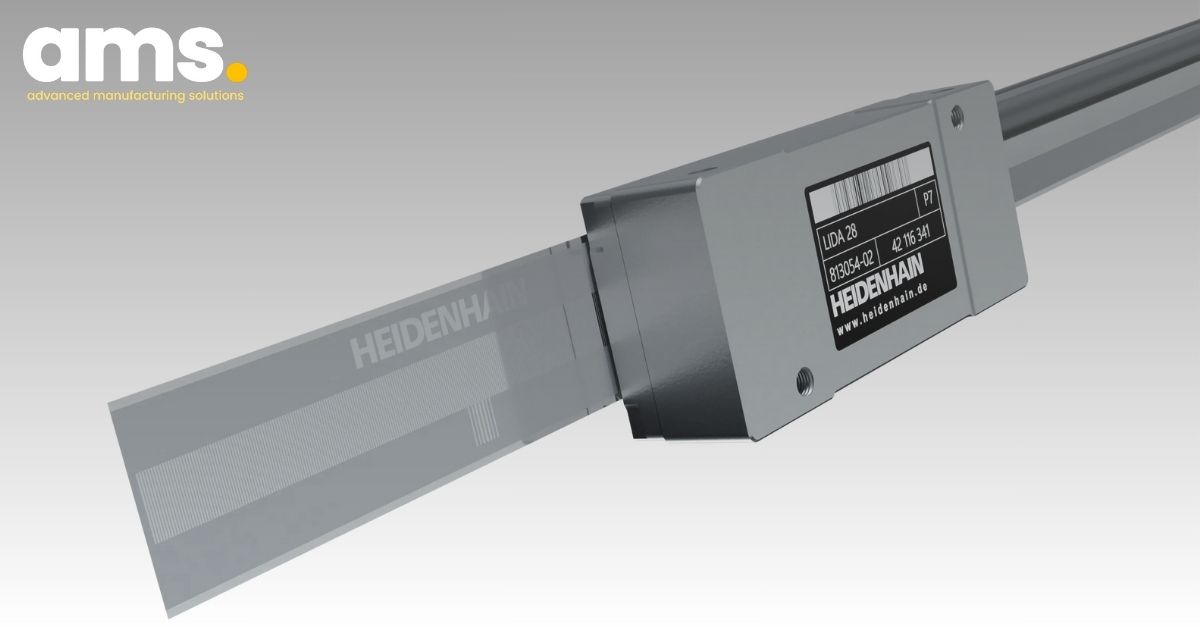
3. Specialty encoder applications for machining
The core principles of encoders persist, involving the measurement of rotational and linear movement as well as position, yet their practical applications are evolving. With escalating demands in the modern market compelling manufacturers to discover more efficient methods of producing intricate components, industrial processes are progressing. Encoders and their uses are adapting to surmount some of the prevailing challenges.
3.1. HEIDENHAIN encoders for robotic machining
Robots utilized in widespread applications like welding, pick-and-place, or vehicle assembly necessitate minimal accuracy demands. Conversely, robotic machining is prevalent in the aerospace industry, as the large scale of components such as aircraft fuselage precludes machining within conventional centers. Historically, this posed a challenge due to the necessity for extreme precision in positioning the tool at the end of an articulated robotic arm, particularly considering the involvement of six axes.
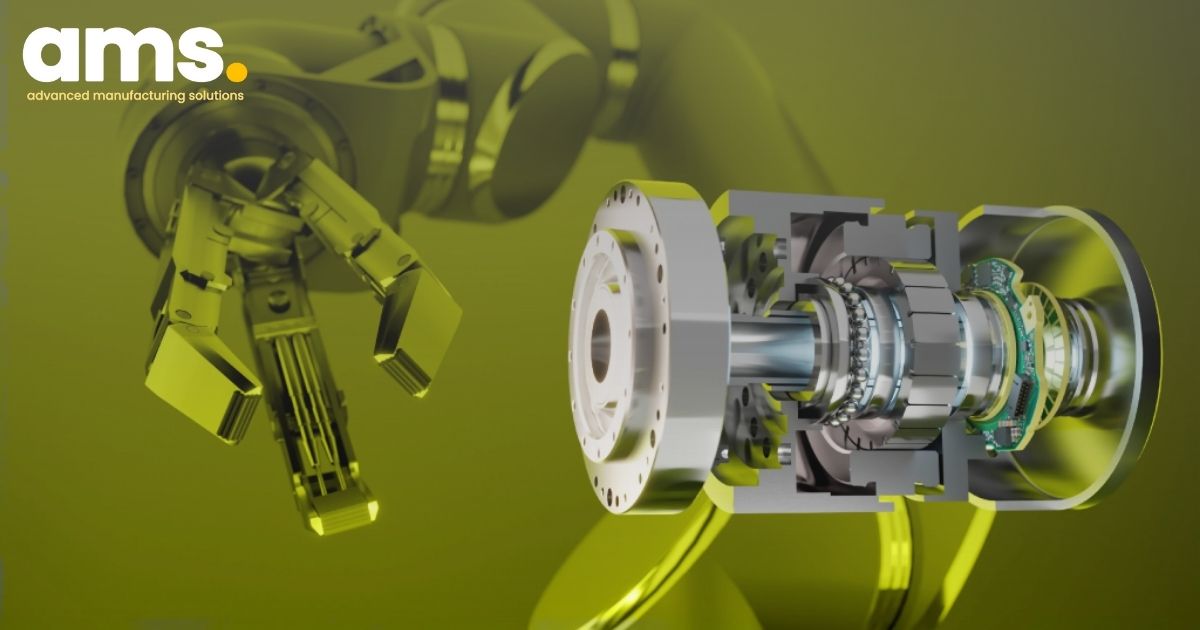
Addressing this challenge, the incorporation of secondary encoders, including the HEIDENHAIN ECA 4000 featuring optical scanning and the HEIDENHAIN ECI 4000 rotary encoder equipped with inductive scanning, mounted after each gear train, enables the capture of the absolute position of every joint. This integration serves to mitigate zero position error and backlash, subsequently reducing imprecision.
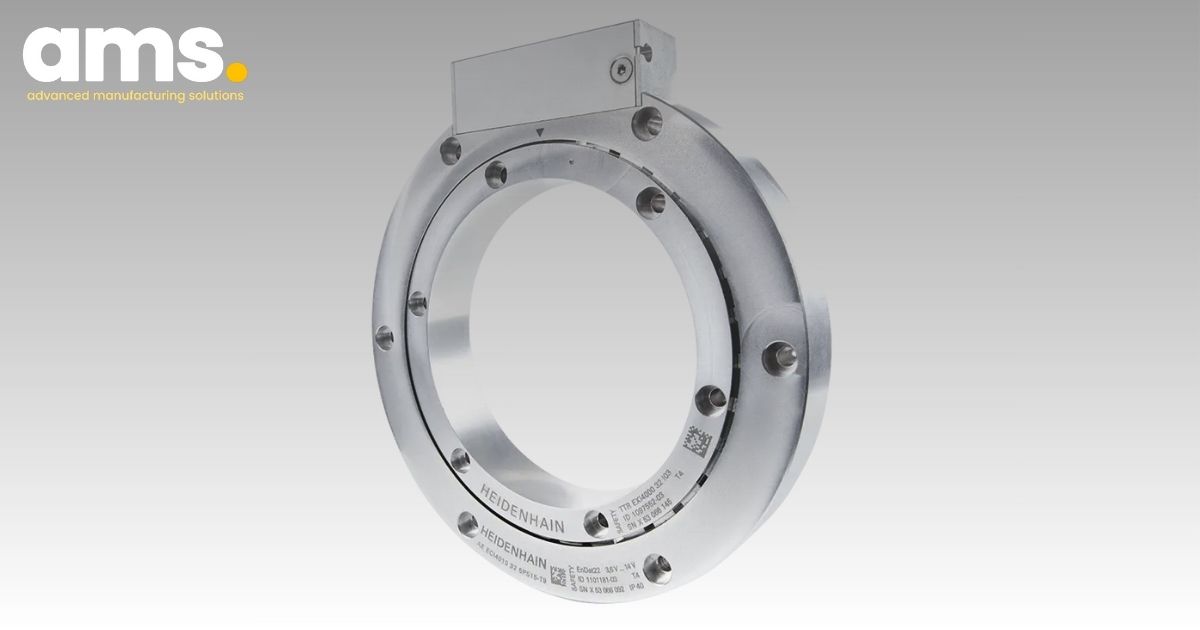
3.2. HEIDENHAIN encoders for testing and calibrating machine tool contour and position deviation
The calibration of machine tools holds pivotal importance in the production of high-precision components utilized in sectors such as watchmaking and optical industries. In order to safeguard optimal machine performance, calibration equipment has advanced, exemplified by the advent of grid encoders that are directly mounted to the work table, allowing for contact-free measurement of machine dynamics. An instance of this progress is the HEIDENHAIN KGM 282, which offers measurements to ±1 µm in the X and Y directions and small signal periods of 4 µm.
4. HEIDENHAIN encoders for functional safety applications
There are numerous factors influencing industrial safety considerations, including the increased speed, power, and flexibility of machines, as well as predictable uptime and regulations. Consequently, functional safety is becoming increasingly significant in the construction and procurement of machine tools. A specialized class of encoders is tailored for safety-critical applications, capable of conforming to SIL 2 (per EN 61 508) or performance level "d" (per EN ISO 13849) in conjunction with a safe control system. These encoders are uniquely equipped for consistent and preemptive diagnostics, as well as secure mechanical connection.
Encoders wield a substantial influence on machining equipment, as the type of encoder installed impacts nearly every pivotal aspect of a machining process including accuracy, speed, safety, setup, usability, and cost. Additionally, encoders are pivotal in driving significant technological advancements. Therefore, understanding the distinctions between various encoder types and their potential applications is crucial for both the development and acquisition of effective machining equipment.
For further exploration of this topic or any other motion control subject, our experts are available for consultation. Schedule a consultation to commence the discovery of specific solutions to your challenges.
5. AMS Company Limited - HEIDENHAIN exclusive distributor in Vietnam
At AMS Company Limited, we are proud to be the exclusive distributor of HEIDENHAIN products in Vietnam. As the leading provider of precision measurement and control equipment, HEIDENHAIN's products are renowned for their quality and reliability. By partnering with us, you gain access to a wide range of HEIDENHAIN encoders suitable for diverse industrial applications.
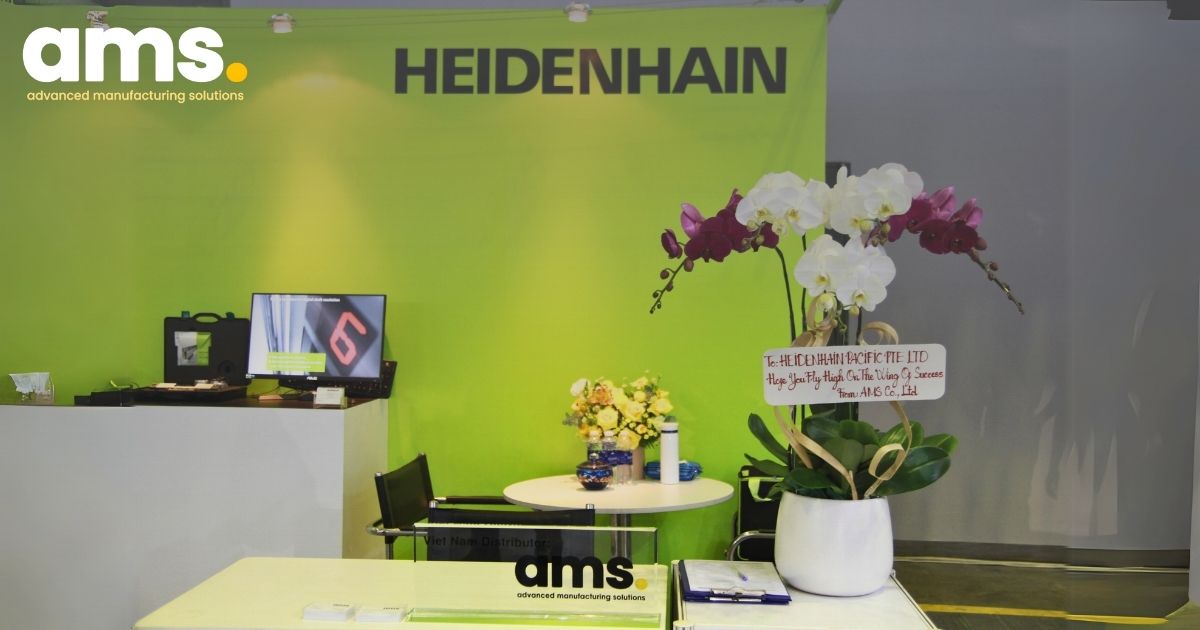
Contact AMS today to receive expert consultation on selecting the right HEIDENHAIN encoder for your specific business needs. Our team of knowledgeable professionals is dedicated to understanding your requirements and recommending the most suitable solutions to optimize your operational processes. Whether you are in the automotive, aerospace, medical, or general manufacturing industry, we have the expertise to guide you in choosing the ideal HEIDENHAIN encoder for your applications.
By choosing to procure your HEIDENHAIN products through AMS, you can also take advantage of HEIDENHAIN's comprehensive warranty and maintenance policy. This means that the products we sell are eligible for coverage under HEIDENHAIN's warranty, providing you with added peace of mind regarding the longevity and performance of your investment. Unlike products obtained from other sources, there is no guarantee that they will be covered by HEIDENHAIN's warranty and maintenance policy. In the event of a malfunction or unexpected issues, it could result in additional costs and disruptions to your operations.
Don't compromise on the quality and reliability of your HEIDENHAIN encoders. Trust AMS Company Limited as your exclusive partner in Vietnam to ensure that you receive genuine HEIDENHAIN products with the backing of reliable warranty and maintenance support. Contact us today to explore our range of HEIDENHAIN encoders and experience the assurance of working with the leading distributor in the region.
AMS Company, Ltd.243/9/10D To Hien Thanh, Ward 13, District 10
Hot line: 028.3868 3738/3903 - Fax: 028.3868 3797
Read more articles
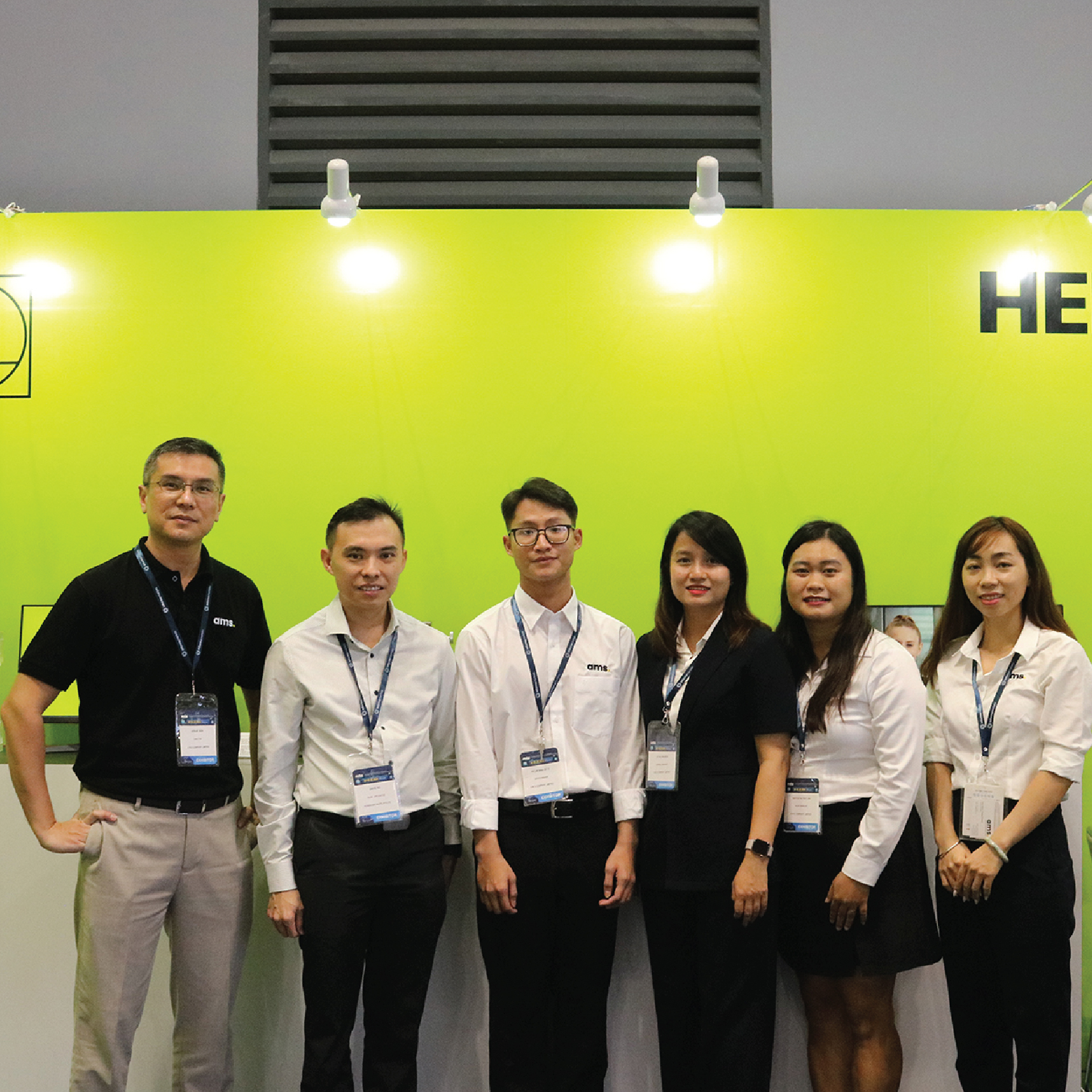
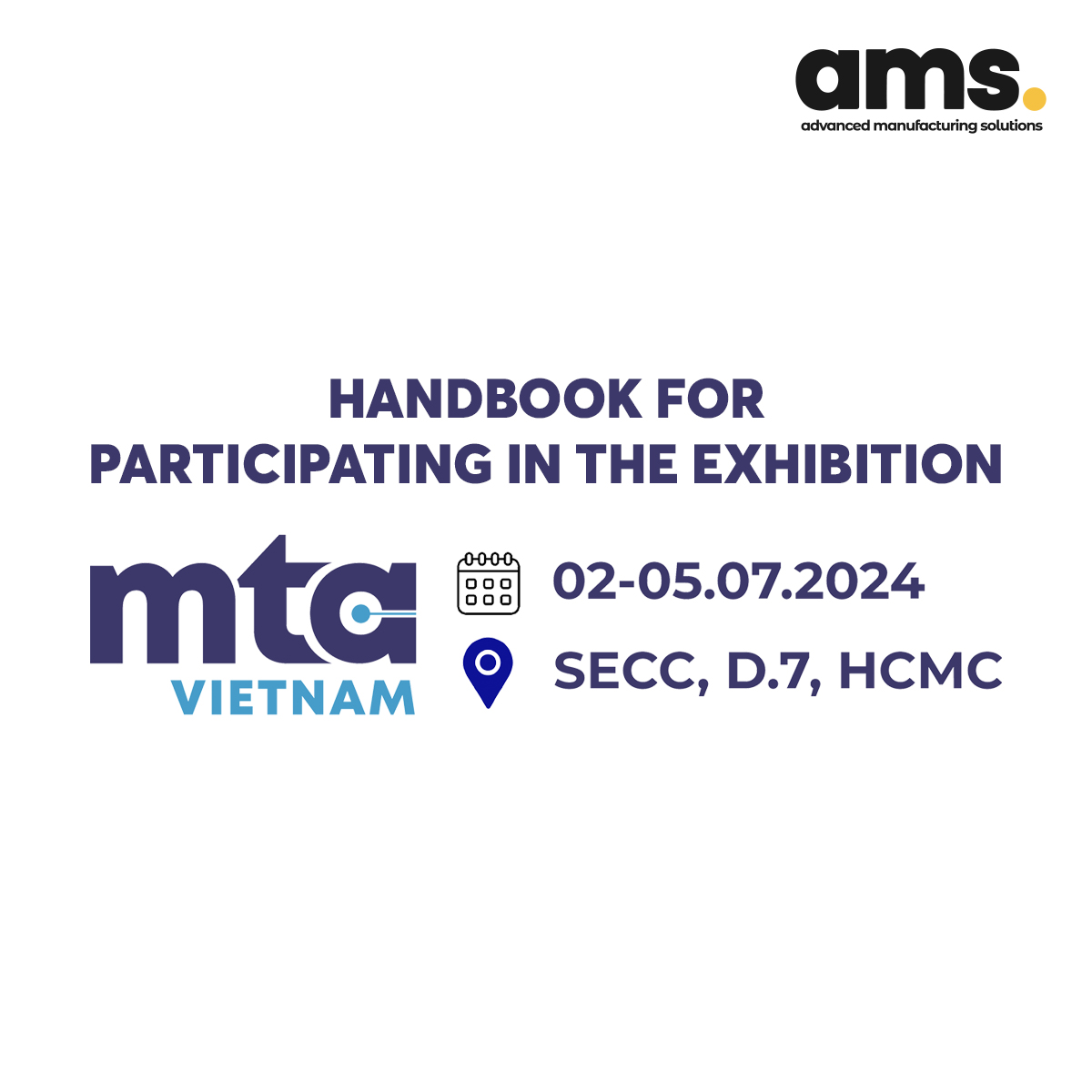
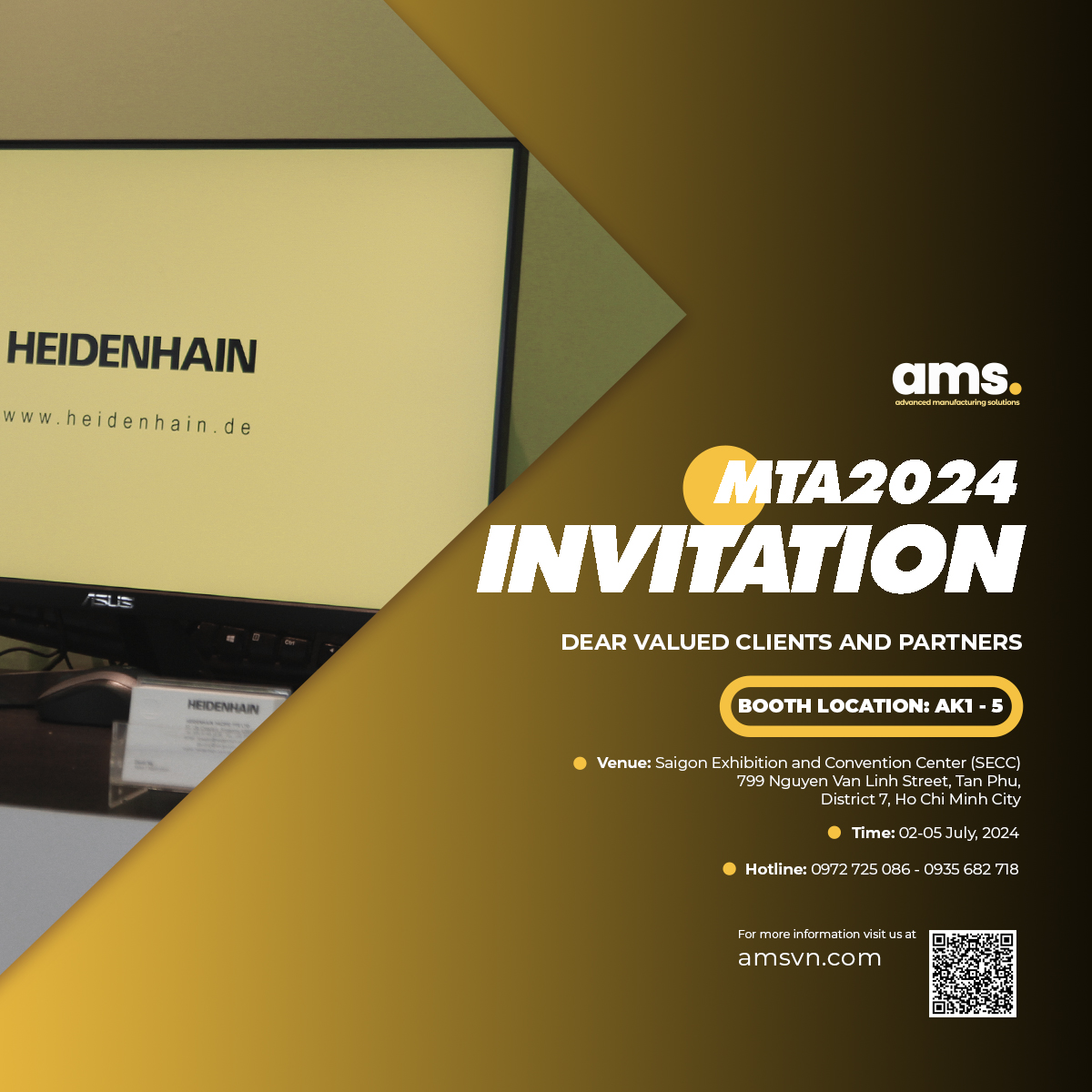